|
The Visitor 6
Watches take shape
|
|
Here, at last, the watches begin to take shape, but before passing
to the assembly stage, the visitor will be shown one of the high-spots
of modern watch manufacture, the Greiner Spiromatic hairspring
vibrating machine, which gives the correct count to the balance
and hair-spring assemblies. The action of the machine is almost
uncanny, for it will unfailingly find the correct pinning point
for the hairspring in a few seconds. All the operator has to
do is to feed its two timing heads with balance-and-hairspring
assemblies by slipping the outer end of the hairspring past a
counting pin and then on between a spring-loaded pressure roller
and a knurled feed shaft. The Spiromatic then takes over, and,
under the control of a quartz crystal time standard, it checks
the time of swing of the balance and spring and automatically
winds in or out the outer coil of the spring until the right
point for correct timekeeping is reached. At that moment, the
alteration of spring length ceases, and a stroboscopic indication
is given that the adjustment has been completed. The other timing
head, which has been loaded during the operation of the first,
is now, in its turn, brought into operation whilst the operator
cuts off the timed spring to length by pressing a cutting lever
that also pre-shapes the outer coil for pinning. This alternate
operation of the two heads of the machine enables about 200 balance
assemblies to be timed in an hour. |
|
The Assembly Line
Just beyond this machine is the beginning of the assembly
line, which is probably one of the best laid out in any watch
factory in the world. As usual, the assemblers sit at benches
arranged at right angles to the direction of travel of the central
conveyor belt. The benches are so well fitted that they would
be the envy of many craftsmen, and a notable feature of their
construction is the cunningly angled arm rests. |
10 1/2 ligne gents wristwatch
assembly |
Assembly
proceeds on what is known as the "sequential batch"
method, the average batch being 50 movements. Everything is done
to simplify each process, and a number of clever tools and fixtures
have been provided to assist with this. Supplies of parts are
held in containers which are arranged in nests facing the assembler,
and the addition of each component during the assembly process
is carried out with a minimum of movement and effort. Movement
assembly follows normal lines, the plate receiving its train,
bridges, escapement, and so on, in stages as it moves along from
assembler to assembler, between each process the movements are
placed in individual containers for their brief journey to the
next assembler and placed on the conveyor. Barriers spanning
the conveyor belt halt these containers at the appropriate point,
and after completing her stage of assembly, all that each girl
has to do is to replace the movement in its container and put
it back on the conveyor on the other side of her particular barrier. |
|
It is an assembly line such as this that the value of the careful
inspection at earlier stages becomes so apparent, for movement
after movement goes through all the assembly stages without a
hitch, and progress is smooth and rapid. Even so, inspection
and testing continues all the way. |
|
An interesting detail is that a dummy winding stem is used all
through assembly, the real one only being fitted at the casing
stage. Very careful checks and tests are applied to the keyless
work. This part of a watch often has to bear the brunt of unskilled
winding or setting. |
|
There are 7 pages on the visit in 1962.
Use the box links below to see the other pages |
 |
      |
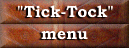 |
|