|
The Visitor 4
Large number of presses
|
|
Pressing
The other basic process of watch manufacture, pressing,
is carried out on a group of presses of several types and of
very different sizes. Some, indeed, seem surprisingly large for
work on watch components. These produce the rough blanks from
which the main plates are made. |
|
Somewhat smaller presses produce other parts, such as cocks,
wheel blanks, keyless parts and so on and in most of these the
"repassing" method is used to ensure accuracy and freedom
from burrs and roughness. When the blanks have been pressed out
from brass or steel strip, they are transferred to a further
pressing process called "repassing". This consists
of passing them through a press-tool that is slightly smaller
than the one originally used to press out the blank from the
strip, and by shaving a further 0.1 mm or so off the edges, it
removes any roughness left by the first, or blanking tool, and
improves the contour. This is particularly valuable in the production
of keyless parts, such as those of the 8 3/4 ligne movement.
Swing-toggle presses are used on the production of bolts and
similar components, and are ideal for the purpose being simple
to operate on such small parts and giving perfect control. Other
small presses operate the familiar two-column press-tools in
the production of bridges, cocks, and similar parts. |
(Left to Right) Mr J. Turley (Toolroom engineer), Mr J.A. Delany
(Asst. Works Manager), and (4th from left) Mr Howard Griffiths
(Security) with visitors from the Imperial Defence College. |
|
|
Recessing
One of the most fascinating processes in the whole
work of production at Gurnos works is "recessing" -
the cutting of sinks in the main plate blanks to accommodate
the train and other parts. After pressing, the plate blanks are
shaved on both faces to give a smooth, even surface, and then
they pass to the recessing machine. This is a very fine example
of modern technique, for it carries out at one time, and in one
setting of the blank, work that formerly required much individual
setting up of the watch plate. On recessing machines, two blanks
are set up on two identical heads on the machine, being located
by the working holes. They are clamped, and the machine starts
up. By means of two single-point tungsten-carbide tools, which
are really tiny end-milling cutters, one for each blank, metal
is rapidly cut away to provide the sinks and recesses needed,
each sink or recess being of exactly the right dimensions and
depth. The cutter, revolving at high speed, moves about in a
most astonishing manner, now moving in to cut a deeper recess,
now following a complex path as it produces some necessary "elbow
room" for a future component, and finally, when all the
cuts are completed, coming to rest automatically. The action
of the cutter is guided by accurately shaped cams, whilst the
depth of the cuts is determined by micrometer stops. The machine
can even be made to cut a perfectly round hole, or to leave a
round peg that is as precise as if it had been turned, just by
suitable shaping of the controlling cams. Added to all this,
the finish left by the cutter is equal to any obtained by turning. |
|
Both surfaces of the blank are recessed in turn. When it passes
on from this section of the factory, it is a blank no longer,
for it is well on the way to becoming a watch plate. |
|
Centre dotting
The next process that the plate encounters is most
important - the centre dotting of the holes that will later carry
pivots, screws, steady-pins, and so on. In fact, the whole accuracy
of the future movement is decided at this stage. Again from a
location given by the two holes in the extremities of the rough
plate, the dots are indented by a tool of extreme accuracy. Each
of the dotting points is precise in position to a tiny fraction
of a millimetre, and, as there may be dozens of them, the setting
out of every separate point with the necessary accuracy and the
subsequent maintenance of that accuracy during the working life
of the tool, call for workmanship of the greatest precision. |
|
Precision drilling
After centre-dotting, the holes for pivots, steady-pins, and
similar items are drilled on sensitive drilling machines, operated
by girls whose deft fingers apply the exact pressure to produce
a perfect hole. How skilled these girls are is shown by the fact
that, although the drills are so small, they hardly ever seem
to break one. Other drilling and tapping operations are carried
out on automatic machines, and some holes which will later have
jewel-holes pressed into them are drilled slightly under-size,
and then enlarged to their final diameter by precise press-tools
of the shaving type. |
|
There are 7 pages on the visit in 1962.
Use the box links below to see the other pages |
 |
      |
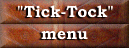 |
|