|
The Visitor 5
Careful inspection at all stages
|
|
Inspection
At every stage of production at Gurnos Works it is
apparent that great care is given to inspection. Special inspection
benches are located at strategic points in the factory, and every
batch of parts is checked and examined by a specially trained
staff armed with accurate gauges and very high magnification
optical
instruments. This sort of check-up takes place many times as
the various component parts of the watch movements pass on, stage
by stage, towards the point where they are finally passed as
correct for assembly. Defective parts are detected astonishingly
quickly, for inspection has the dual purpose of preventing incorrectly
made components from passing to assembly, and of locating the
error in manufacture which caused them. |
|
Wheel and pinion production follows the accepted lines, and is
maintained at a high standard. Wheel blanks are produced from
high-quality strip by press-tools that deliver a particularly
flat and burr-free output, and after careful inspection, these
blanks are mounted on special group-fixtures and cut in batches
on automatic machines, a long line of which is kept busy with.
this work. One of the most fascinating experiences of the whole
tour of the factory is to watch a batch of wheel blanks gradually
acquiring their teeth. |
|
Pinions and escape wheels are cut on indexing machines. The pinion
blanks from the automatic lathes are set up and cut with precision
and speed. |
|
Jewel setting
Every process has something of interest for the visitor, but
it is only possible to select a few for brief description. Jewel
setting is one, for it is a triumph of good tooling. The setting
for the pressed-in jewel is cut to the exact size, and the jewel
placed in position by a girl and pressed home by a small, accurately
controlled press so swiftly that a number of jewels have been
inserted into their plates or bridges before the onlooker has
followed the details of the operation. |
|
Storage
The finished part stores is attractive to anyone with a tidy
and methodical turn of mind. Large quantities of parts are stored
in glass jars which make some sections look rather like a sweet
shop. Each calibre of watch has its own colour-code, which appears
on each jar or storage bin (some parts, obviously, do not lend
themselves to storage in jars) and, indeed, on all labels, tools,
drawings, etc. relating to that particular calibre. |
|
Storage of parts is carefully arranged to give maximum accessibility.
Issuing is done in batches, the method of counting small parts
usually being by weight on precise ratio scales. In operating
these, a sample part is placed in the "ratio" scale-pan
to act as a standard of reference, and the parts to be issued
are then piled into the weighing pan until the scale indicates
that the correct number has been reached. |
|
Another type of scale used is the "Shadoweight", in
which the reading is given by the movement of an optically projected
shadow over a scale, and this gives great precision. It is used
for a very small components, and it operates on the counterbalance
principle. |
13 ligne gents
wristwatch assembly |
|
|
Assembly
In any watch factory, however, the supremely interesting point
is the assembly department where all the planning and precise
work devoted to the various component parts becomes centred in
the working, time-measuring movements. At the Gurnos Works, this
division of the factory really is a division, housed in a separate
semi air-conditioned and dust-proofed two-storey building behind
the machine shops. There is even a small ceremony before one
enters, for everyone must (this is an order) put on overshoes
that are designed to prevent any dirt that may linger on even
carefully-wiped shoes from reaching the spotless floors. |
|
There are 7 pages on the visit in 1962.
Use the box links below to see the other pages |
 |
      |
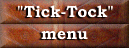 |
|